The big bamboo
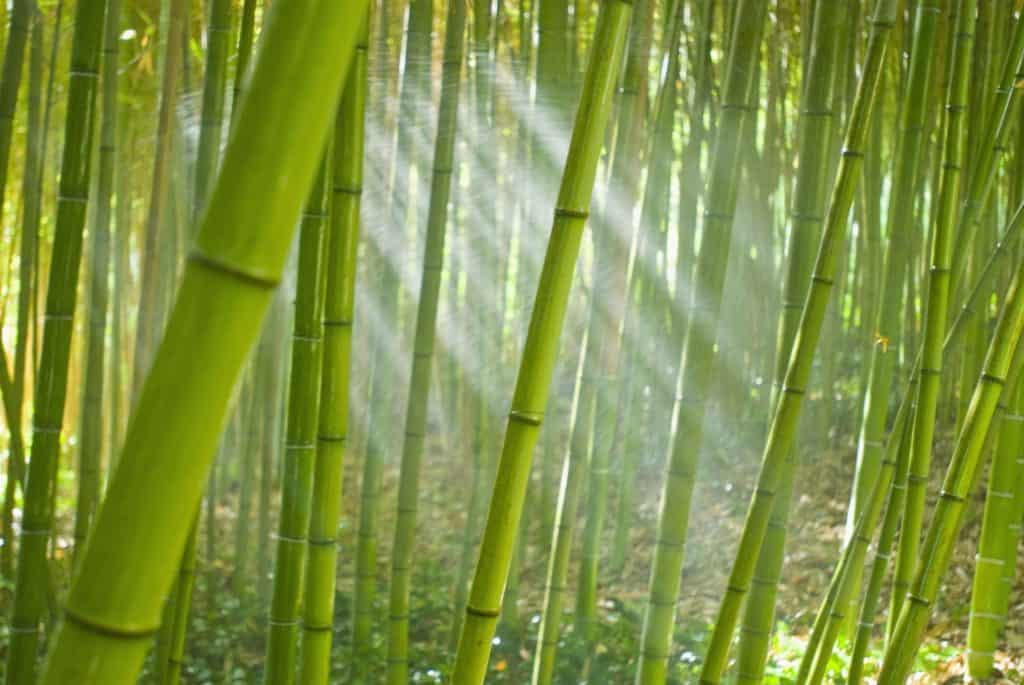
Bamboo has established itself as an excellent material for bike frames. Not just because it is light and robust, but especially for its vibration absorbing qualities. Bamboo bikes tend to be stiff, light, and incredibly comfortable to ride. The bamboo is not sensitive to impact from the outside and will not develop dangerous cracks if wrecked or dropped. Bamboo bikes can be used daily in all weather. The natural outer surface of bamboo is robust and insensitive to scratching or abbrasion, and only needs to be waterproofed with an additional layer of plant-based varnish to withstand years of intense use.
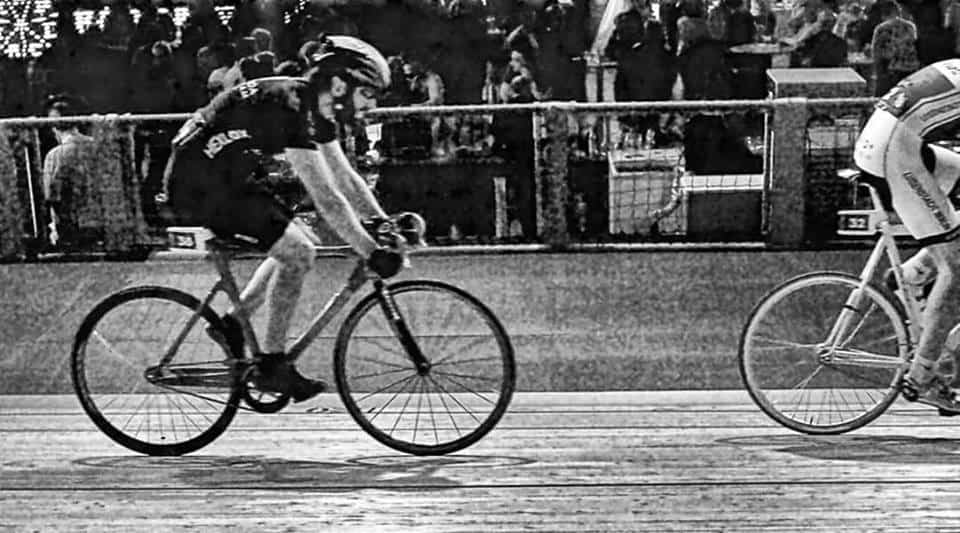
The secret to these incredible properties lies in the fractal structure of the bamboo fibers within the hulm. The most dense, stiffest fibers are bundled close to the outside where they have the most effect on tensile strength. Progressing toward the inside of the wall thickness, the fibers become less dense, provide compressive strength and vibration absorbtion. There is no technology currently available to mimic this fractilic structure within a composite tube, much less in every concievable dimension, at an affordable price, available worldwide in unlimited quantities and ecologically friendly.
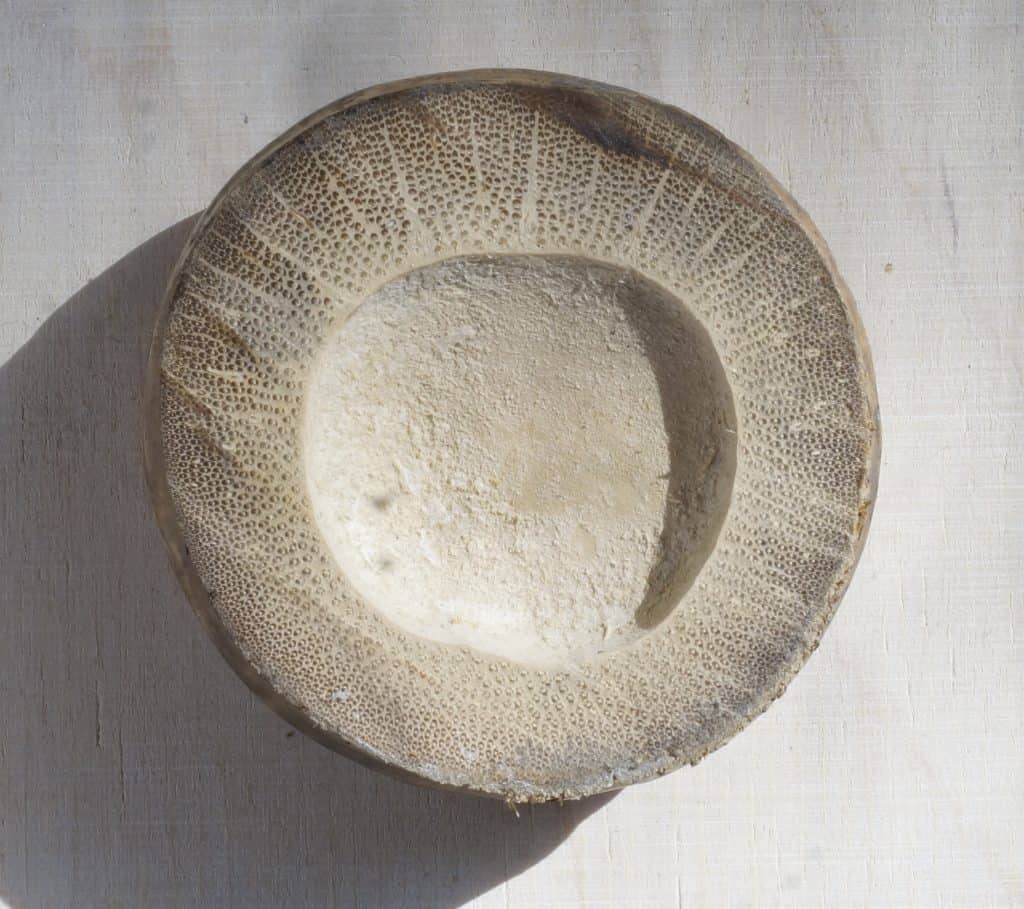
When compared to other bike frame materials, bamboo most closely resembles high-end steel tubing. The tensile strength, stiffness, and usability of bamboo and steel match eachother so well, that many first time riders of bamboo bikes cannot identify the difference. Steel however has one main downside over bamboo: the available tubing diameters. The outer diameter of a tube is its most significant mechanical property, but due to economic constraints, high-end steel tubing is produced in only a few diameters. This limits its use for many purposes including high performance track bikes and larger-than-average frames.
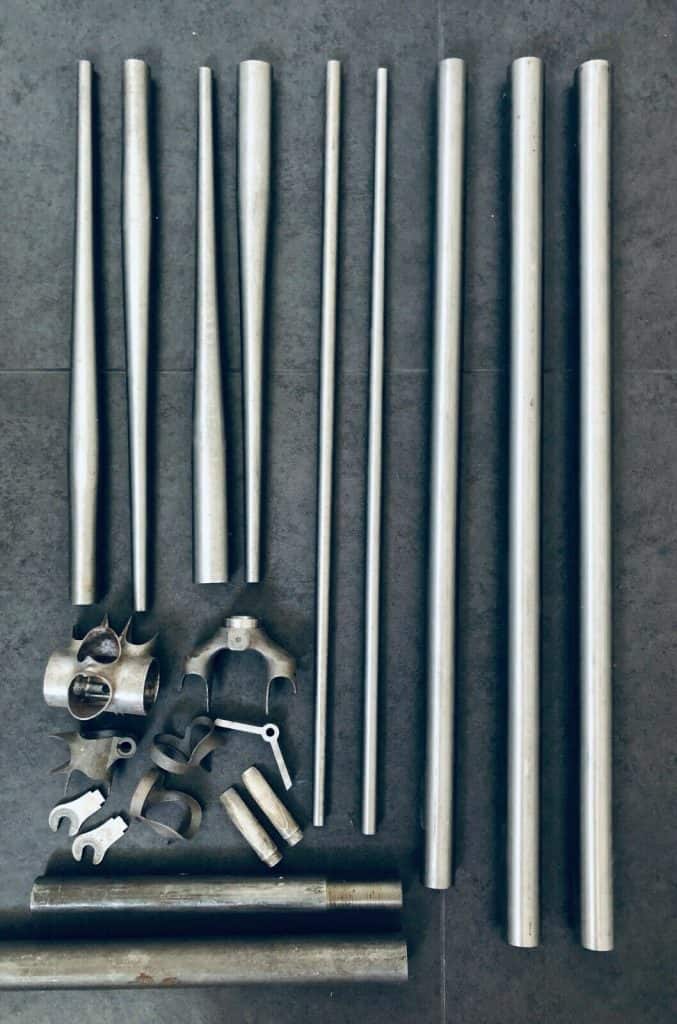
The variation in diameter and wall thickness available in bamboo allows for incredible creative freedom when designing a custom bike. It also allows for excellent suspension-like charictaristics in cargo bikes which cannot be matched by any other material. Ozon cargo bikes are lighter than competing aluminum models and have better vibration absorbtion.
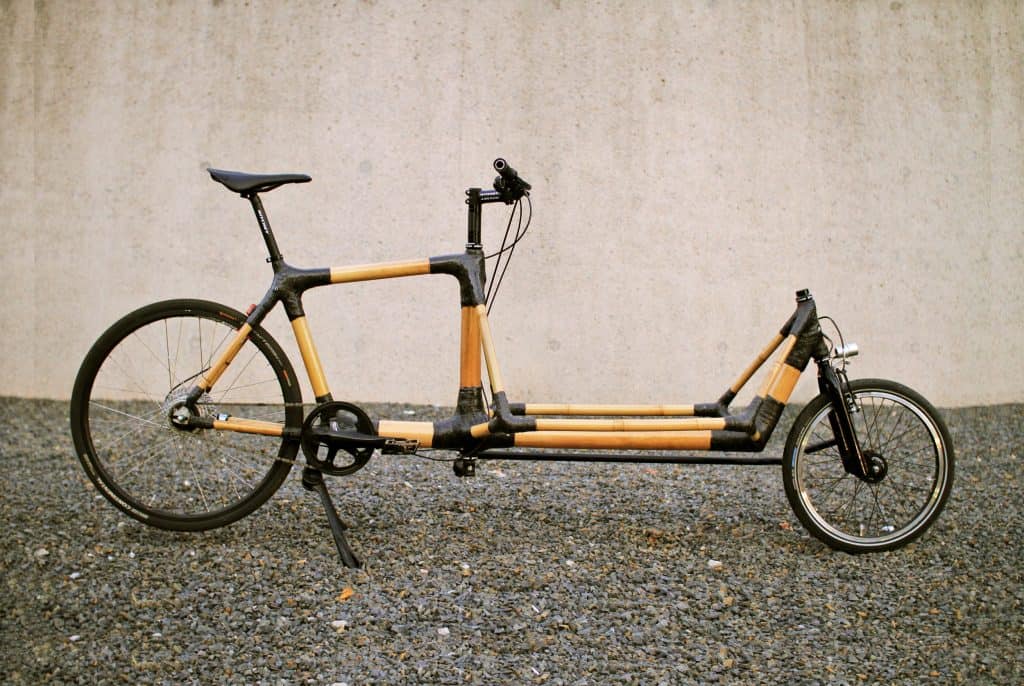
No steel tubing exists that can provide the light weight and outer diameter needed for cargo bikes, as this would lead to an impossibly thin wall which would not be usable in the real world. Thus cargo bike manufacturers rely on Aluminum tubes which do not provide the desirable flexibility of steel tubing. This flexibility is an advantage for heavily loaded cargo bikes, which benefit from its suspension-like effect. Bamboo however fulfills this need flawlessly, with tubing available in diameters far exceeding that needed for cargo bikes, with a weight advantage over aluminum and vibration absorbing flexibility which even surpasses that of steel.
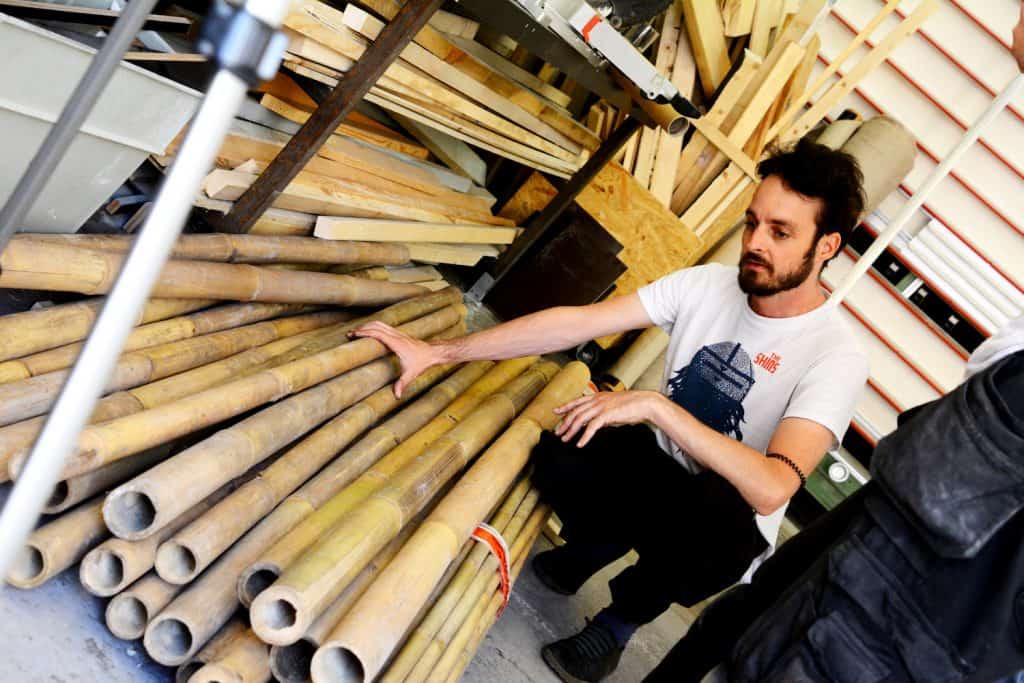
For the joints we use Flax fiber composite, a carbon-fiber-like material that matches the E-module and temperature expansion charactaristics of bamboo. The use of composite joints also allows for both creative and engineering freedom: you can strengthen or lighten different parts of the joint as needed simply by altering the number of layers of composite cloth used.
Ozon has partnered with the University of Eberswalde to test the strength of our bamboo-composite material combination. The results of the tests are confirmed by real world experience: many Ozon bikes have been ridden thousands of Kilometers of many years, and are still going strong.
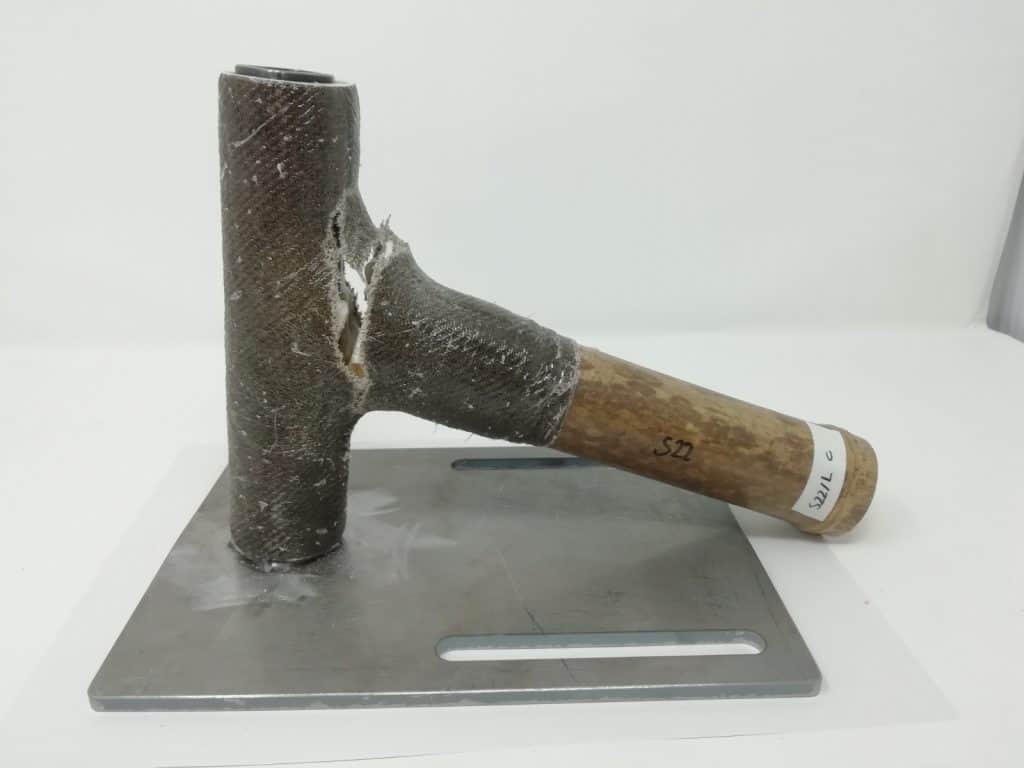
The fiber layup of Ozon bikes is not random. We have an exacting protocol of exactly how many layers to put where. This comes both from testing and experience, and has proven itself to make longlasting frames. The exact fiber layup protocols for each bike design are found in the Ozon tuturial videos.
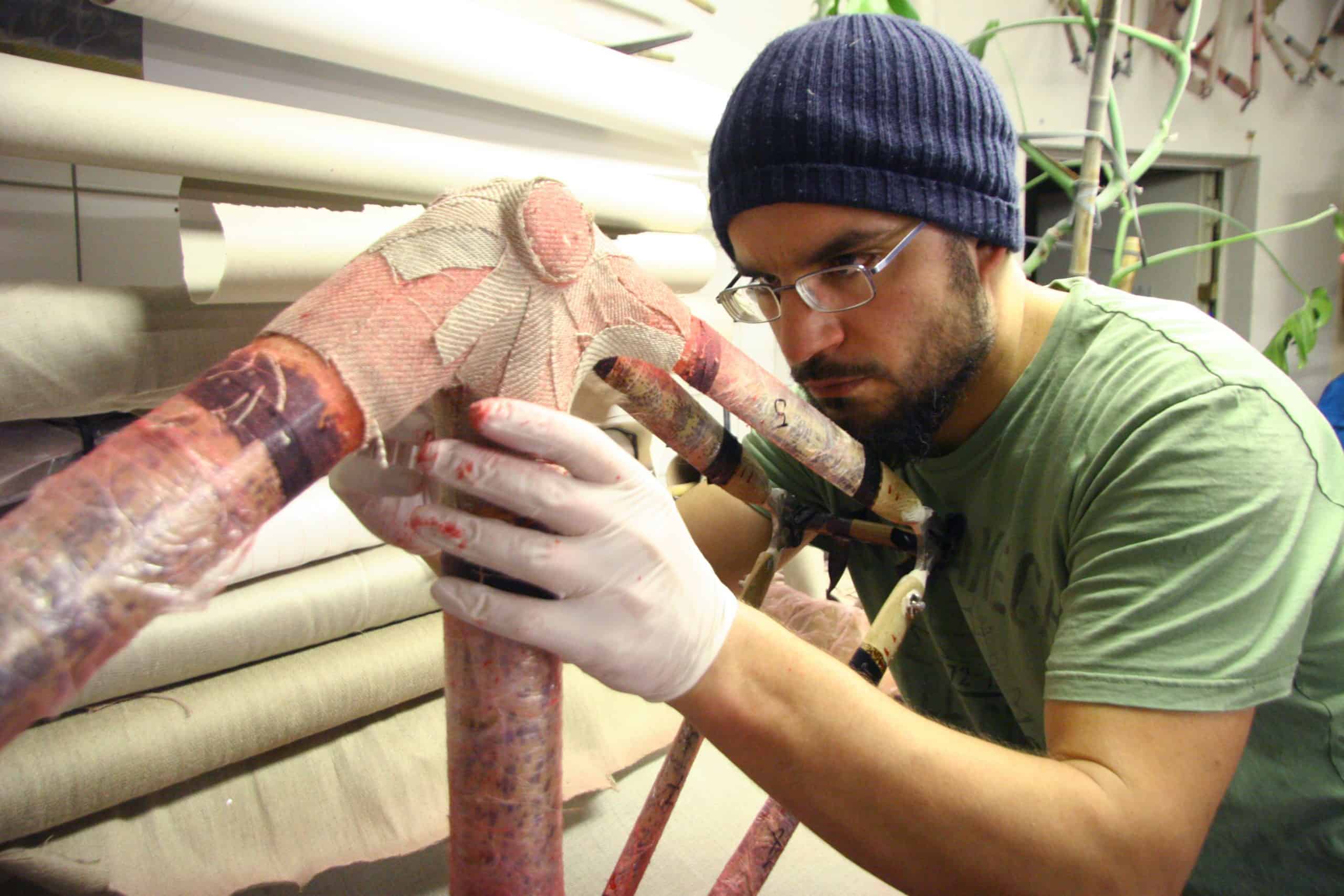
For all you hardcore gearheads out there who like facts and numbers and stuff, check out the following links. Below are citations from these links, written by Christoph Tönges of CONBAM and the University of Aachen.
https://bambus.rwth-aachen.de/eng/reports/mechanical_properties/referat2.html
http://conbam.info/pagesDE/properties.html
The bamboo is in its size, lightness and strength an extreme product of nature. It is stable and because of its cavities an extreme light and elastic building material. The reinforcement by diaphragms and its physical conditions cause its enormous superiority compared to other building materials.
Throughout the world there are about 500 different species of bamboo sometimes within hundreds of subspecies. Even only in Colombia about 25 different giant bamboos are used for construction. To those belongs also the “guadia angustifolia” which we look at in this article. It grows in hights up to 1800 metres [NN], mostly in small forests along creeks but also on fields and inclinations. There exist two subspecies called guadua castilla andguadua mecana. It reaches a tallness of about 20-25 metres and a diameter up to 18 cm.
Each stem grows out off a netkind rootsystem and reaches already after one year its total tallness. After that the [leitsysteme] start to lignify and in the next 6-8 years it gains harness and strength because of the silification of the outer tube wall. So bamboo can also be titled as a lignifying giant grass.
The lignifying cell construction of the bamboo texture and its technical conditions are very similar to the original texture of wood. Whereas wood has got a hard centre [Hirnholz] and becomes weaker towardsthe outer parts [Splintholz], the bamboo is in its outer parts hard and in its inner parts weak, what causes a much more stable construction. From the inner parts of the tube towards the outer parts you can realize a continious accumulation of the[Leitbündel]. The more stable fibre structures are most dense where you find the strongest statical stress.